Digitalisation of manual processes increases operational real-time visibility and makes it easier for our customers to do their jobs efficiently and correctly.
The Industry 4.0 digitalisation capabilities
Paperless digital reports
Allows instant access to reports from various data sources and devices, facilitating quicker decision-making and collaboration, and reducing paper usage.
Data acquisition
Gathers data using industry-standard protocols and industrial internet of things frameworks for asset analysis and aggregates data from multiple sources in the cloud for advanced analytics and storage. This enables scalability and remote access.
Operational technology – information technology integration
Streamlines processes by integrating manufacturing operations and IT systems, reducing manual interventions and optimizing workflows
Laboratory information management system
Integrates with laboratory instruments and automates routine tasks, reducing manual work, minimising errors and ensuring quality throughout the manufacturing cycle.
Production monitoring and process tracker
Provides real-time updates about production, downtime and rejection, facilitating comprehensive product genealogy, including forward material tracking and reverse traceability throughout the process.
Predictive modelling and golden batch visualisation
Incorporates AI technologies into manufacturing to visualise and support data-driven decision-making.
Maintenance management
Facilitates plant maintenance, preventive management, asset management, predictive management
Utility and energy management
Uses systems to track energy usage and utility performance in real-time, allowing for immediate adjustments and proactive maintenance.
Manufacturing and logistic process automation
Evaluates current assembly processes, identifies bottlenecks and defines automation goals.
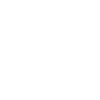
Challenges
- Inability to track process parameters
- Encountering issues in batch process transparency
- Delay in processes, since the entries previously were done manually
- Maintenance of the process parameter data was not accurate in the equipments
- Facing issues with alerts and daily e-mails
- Integrate OT and IT systems
- Develop and implement API integrations for custom applications
- Conduct data verification through collaborative checks and custom reports
- Create custom development solutions including tailored forms and reports
- Perform rigorous testing with comprehensive test cases and verification
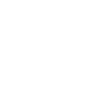
Strategies and solutions
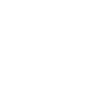
Key benefits
- Monitor in real-time: by tracking production, raw material intake, and in-process QC data.
- Capture energy and utility parameters: by recording energy and utility metrics.
- Track finished goods: by monitoring the status and inventory of finished goods.
- Implement an automated log-sheet: by ensuring automated logging of relevant data.
- Generate customised reports: by creating daily reports on production vs. consumption, stock levels, norms, OEE (Overall Equipment Effectiveness), and utilisation.
- Conduct Six Sigma analysis: by improving the process quality through detailed analysis.